I got sidetracked by the Mario Grandi thing, but wanted to get this down so I'd actually have to follow up later with more detail...likely more than you ever wanted to know or whatever.
Yesterday I ordered a pipe kit from Mark Tinsky over at the American Pipe Smoking Company ...site...place...thing...whatever! I thought it might be fun and instructive to sort of 'blog' the experience (in moderation) for other guys that have considered making their own pipe.
So I have one on the way. It will be my fourth or fifth kit. The first were all generic kits from generic vendors. They turned out fine, and since I'm a carver (walking sticks, canes, other bizzare stuff) that part was easy...in fact it took over (like it usually does with me) and the pipes turned out to be more 'carving projects' than pipe projects. Which is fine...but this time a wanted to end up with a classic item.
After a little looking around I settled on Mark's system as being exactly what I wanted. Mark requests lots of detail, photos, etc. so he can (get this) pick the most appropriate block and bore the holes in just the right way to be perfect for you. So, like, don't change your mind about your project mid-way or you're TOAST! lol Anyway, I ended up with the largest size chunk of platteau you can order (Mark's direction) and for the same cost as most anyone else charges for something I guess they just find under a tarp in the back of warehouse (blah, blah, blah) I get a block drilled specifically for my intended design...an oversized Poker.
This is what's on its way...but with a different stem:
As I go along I'll try to provide a reasonable series of pics so there's SOME level of visual interest. Other than that I'll keep things to a minimum, describing what I'm doing and anything that comes up I think others would want to know re: tools, materials, processes, etc.
BTW: Mark indeed lives up to his reputation. Easy to work with, good information, super fast service...speaking of which, get this: I first contacted him let's say on a Wednesday...placed the order the next day...that same day he selected and drilled the block and on the day after it was in the mail and on its way. OK - I'm officially amazed.
More to come.
Yesterday I ordered a pipe kit from Mark Tinsky over at the American Pipe Smoking Company ...site...place...thing...whatever! I thought it might be fun and instructive to sort of 'blog' the experience (in moderation) for other guys that have considered making their own pipe.
So I have one on the way. It will be my fourth or fifth kit. The first were all generic kits from generic vendors. They turned out fine, and since I'm a carver (walking sticks, canes, other bizzare stuff) that part was easy...in fact it took over (like it usually does with me) and the pipes turned out to be more 'carving projects' than pipe projects. Which is fine...but this time a wanted to end up with a classic item.
After a little looking around I settled on Mark's system as being exactly what I wanted. Mark requests lots of detail, photos, etc. so he can (get this) pick the most appropriate block and bore the holes in just the right way to be perfect for you. So, like, don't change your mind about your project mid-way or you're TOAST! lol Anyway, I ended up with the largest size chunk of platteau you can order (Mark's direction) and for the same cost as most anyone else charges for something I guess they just find under a tarp in the back of warehouse (blah, blah, blah) I get a block drilled specifically for my intended design...an oversized Poker.
This is what's on its way...but with a different stem:
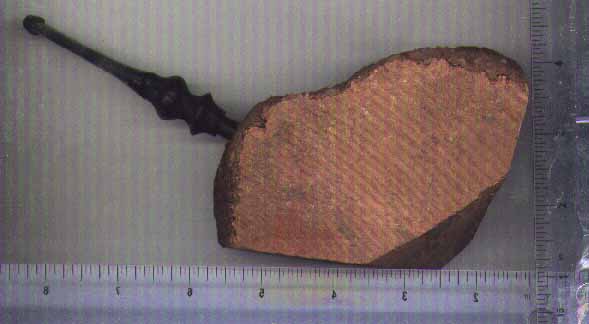
As I go along I'll try to provide a reasonable series of pics so there's SOME level of visual interest. Other than that I'll keep things to a minimum, describing what I'm doing and anything that comes up I think others would want to know re: tools, materials, processes, etc.
BTW: Mark indeed lives up to his reputation. Easy to work with, good information, super fast service...speaking of which, get this: I first contacted him let's say on a Wednesday...placed the order the next day...that same day he selected and drilled the block and on the day after it was in the mail and on its way. OK - I'm officially amazed.
More to come.